User:John Cummings/Archive/Tesla
{{Infobox industrial process | name = [[Tesla Model S]] manufacturing process | image = Tesla auto bots.jpg | caption = A robot installs the [[laminated glass]] roof of the [[Tesla Model S]]. | type = physical | sector = Automobiles | technologies = Electric vehicles | feedstock = Aluminium, Steel | product = [[Tesla Model S]] | companies = [[Tesla Motors]] | facility = [[United States]]: [[Fremont, California|Fremont]], [[California]] ([[Tesla Factory]])<br />[[Europe]]: [[Tilburg]], The [[Netherlands]] ([[Knock-down kit|all parts]]) | inventor = | year =2012–present | developer =[[Tesla Motors]] }} {{Commons category|Tesla Motors}} The Tesla Model S manufacturing process uses more than 160 specialist robots.[1] Many of the Model S's unique components, including the battery pack, battery module, and drive units are manufactured in-house. The plant has a high level of integration compared with other modern car assembly plants, with most processes taking place within the Tesla Factory. This includes most of the stamping and machining, painting, and some coding. Design engineers also work at the factory itself, rather than a separate facility.[2]
Each vehicle is made to order with a two to three month wait time for delivery,[3] although individual vehicles only take between three to five days to complete the production process.[1]
Production facilities[edit]

The Model S is constructed at the Tesla Factory, an automobile manufacturing plant in Fremont, California, US, and the principal production facility of the Tesla Motors Tesla Model S. The facility was formerly known as New United Motor Manufacturing, Inc. (NUMMI), a joint venture between General Motors and Toyota.[2][4] The plant is located in the East Industrial area of Fremont between Interstates 880 and 680 and employs around 3,000 people.[1]
For the European market, Tesla assembles and distributes from its European Distribution Center in Tilburg, the Netherlands.[5] Cars are built and tested in Fremont, California. The battery pack, the electric motor and parts are disassembled and shipped separately to Tilburg, where the cars are reassembled.[6] The center occupies a 203,000 sq ft (18,900 m2) industrial building that also serves as a workshop and spare parts warehouse.
Drive unit construction[edit]
Motor construction[edit]
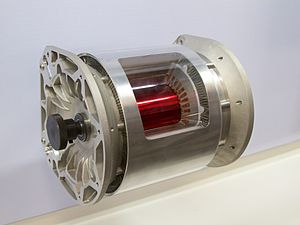
The alternating current electric motor is constructed in-house. The main components of the motor are the stator and rotor.[7]
Stator construction[edit]
The motor construction begins when a robot unspools and winds over 1⁄2 mile (0.80 km) of copper wire per motor. It then pulls the copper wire into a stack. The motor has three phases and so requires three coils of copper.[7] A worker then lengthens and straightens each bundle of wire and inserts the hydraulic lift to transfer the motor to the next station.
A worker insulates each bundle of copper wire in a plastic sleeve to prevent the bundles from touching one another. The ends of the bundles are then snipped to the correct length. Lugs are added and crimped to form attachment points for the motor's three phases.[7] A specialized automatic sewing machine then binds the coils together to keep them in place, the increased tightness of the binding provided by n robotic sewing machine increases the efficiency of the motor. The stator is then encased in a two part epoxy resin to help in evenly distributing the motor's heat. The stator is now complete and is inserted into a heated metal case, locking the stator inside as the case cools.[7]
Rotor installation[edit]
A technician uses a hoisting system to insert the rotor inside the stator completing the construction of the motor.
Additional drive unit components[edit]
A worker then installs the differential and other sections of the gearbox attaching it together using bolts, an air leak test is then conducted. The three phase tripole power inverter is then installed onto the top of the motor to convert direct current from the battery into alternating current for the motor to use. The motor then undergoes a series of automated tests taking 4 minutes to ensure correct function and moved to the general assembly area to be installed into the car.[7]
Battery pack construction[edit]

The Model S 85 has the highest range of any production electric car at 265 miles (426 km).[2] Its battery pack contains 7,104 '18650' lithium-ion battery cells in 16 modules[8] wired in series (14 in the flat section and two stacked on the front).[9] Each module contains six groups[10] of 74 cells[11] wired in parallel; the six groups are then wired in series within the module.[11][12][13][14] As of June 2012[update] the battery pack uses modified Panasonic NCR18650A 3100mAh cells with nickel-cobalt-aluminum cathodes.[15][16]
The use of commodity cells is in contrast to every other electric vehicle manufacturer who use specialised large format Li-Ion cells similar to those found in laptops and mobile phones.[17] The liquid-cooled battery pack uses an intumescent gel to aid in fireproofing and even heat distribution.
Body construction[edit]
Aluminium coil blanking[edit]
98% of the Tesla Model S body is constructed from aluminium[7] and is produced from between 50 to 60 coils of aluminium, which weigh up to 20,000 pounds (9,100 kg) each. The coils are unwound, flattened and cut in a blanking machine; additional cutting is also done using laser cutter. The total weight of the aluminium used in the Model S is around 410 pounds (190 kg).[1]
Tandem press lines[edit]
A robot then transfers the aluminium blanks into the tandem press lines where the sheets are stamped into the various panels of the cars. The presses use up to 11,000 ton-force to form the body panels; the upper section applies 1400 tonnes of downward force and the lower section 130 tonnes.[7] The blank aluminium sheet aluminium is stretched over the lower draw die and openings are cut with robots transferring the panels between processes. The workers then inspect each panel to ensure correct pressing, the parts are then stacked in frames and stored. The machines press one part every 6 seconds and create 5,000 parts per day.[1]
Body assembly[edit]
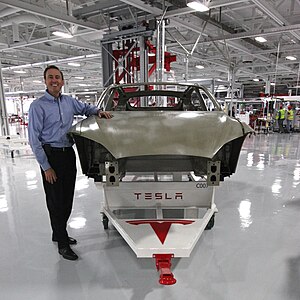
The body panels are transferred to the body centre where they are assembled to create the body of the car. Parts are joined using a five different processes:
- Cold metal transfer welding
- Delta spot welding
- Structural adhesives
- Electric resistance welding
- Self-piercing rivets[1]
Underbody[edit]
The underbody is the main floor system of the car is attached to the frame, the front, centre and rear floor panels are added to the frame by robots and then joined using cold metal transfer welding.[1][7]
Body panel installation[edit]
The body is then transferred down the line on a conveyor where a pair of robots simultaneously install the body sides including inner steel reinforced B pillars, the sides are joined by a pair of headers which span the width of the car, a robot then installs the front end of the car. Workers then use a gantry mounted assisted lifting system to move the doors which are installed using electric drivers, two hinges on each door attach using four bolts, they then attach the front fenders and the hood.[1]
Body in white[edit]
The body is now assembled, at this stage of the manufacturing process the car is referred to as a body in white. A technician inspects the vehicle, checking the fit and finish and all structural adhesive and weld points. A large robot then picks up the completed body and transfers it to a conveyor belt to start the painting process.[1]
Painting[edit]
The body goes through a series of pretreatment processes where it is washed and prepared for painting. The body is then painted by robots able to operate in a cleanroom environment, first using a corrosion resistant electrolytic coating, followed by a primer, then base coat and finally a clear coat. The whole painting process takes 6 hours.[1] The body is then inspected by three teams to ensure the processes have been completed successfully. The body is then transported to the general assembly section by transport robots which use magnetic lines in the floor to navigate.
General assembly[edit]

The car now moves through general assembly, where construction is completed. Once this has happened, the only processes left are testing. Battery-powered carts known as SmartCarts carry the Model S through the general assembly process which are guided by magnetic strips in the floor.
The car is raised on a hydraulic lift to provide easy access to the underside of the car. Technicians then install tubes that will carry battery coolant to cool the battery when the car is operational, they also install the high voltage cables that will transfer electricity from the battery to the motor.[7] The car is lowered from the hydraulic lift onto the electric cart which moves the car body to the next section where a robot installs the car's roof.[1]
Instrument panel[edit]
The instrument panel frame is constructed from steel to provide a higher structural integrity than aluminium. The components are first bolted on to the frame which include:
- Radio tuner and amplifier
- Airbags
- Air vents
- 17 inch touchscreen
- Instrument cluster screen
- Dashboard
The instrument panel is then installed in the car by workers using a hydraulic hoist system and a steering wheel is then added.[7]
Car seats and windscreen[edit]
The interior of the car is installed by both robots and workers. A robot then installs the car seats, it then changes tool heads and picks up the windscreen, applies glue to it and then fixes it to the body of the car and repeats the process with the rear glass.[7]
Drive unit installation[edit]
The car is raised and the drive unit is installed into the rear axle assembly. Because the drive unit provides power directly to the wheels a drive shaft is not needed.[7]
Battery installation[edit]
The battery weighs almost 1,200 pounds (540 kg) and is delivered to the installation area by SmartCart and is raised into the car using a lift. Placing the battery pack under the cabin floor adds strength and rigidity to the car and lowers the vehicle's centre of gravity.[7] A titanium plate is installed over the battery pack which protects it in the event of a high-speed collision.
Wheel installation[edit]
Forged aluminium wheels are then installed while the car is raised, the nuts on the wheels are tightened simultaneously using specialist ceiling mounted equipment.[7]
Final inspection[edit]
The production of the car is now complete, it is now transferred to a section of bamboo flooring for final inspection.[7]
Testing[edit]
The car undergoes a series of quality control tests to assess function, fit and finish. The testing processes take a total of 5 hours; because the car has no emissions these test can be done inside the factory.[3]
Vehicle drive test[edit]
The vehicle test drive consists of driving 20 miles (32 km) on a rolling road at a maximum of 80 miles per hour (130 km/h). In contrast to other cars at this point of the manufacturing process no emissions test is performed because the car produces no emissions. The test is used to:[3]
- Checking the vehicle's anti-lock brakes
- Set the wheel alignment
- Exercise the drive mechanics and motor function
Water test[edit]
The car is sprayed with 228 high pressure jets using 1,500 US gallons (5,700 L) of reusable water to check the car is water tight.[3]
Shake and rattle tests[edit]
The shake and rattle test car is driven over 6 different road surfaces to check there is no abnormal cabin noise:[3]
- Rope road
- Speed bumps
- Cobble stone
- Wave road
- Belgium blocks
- Department of Transportation road
Test track tests[edit]
A thorough road test is performed on the Tesla motors test track.[3]
Final inspection[edit]
Final inspection consists of 101 checks which include:[3]
- Power windows
- Automatic door handles
- Door mechanics
- Touch screen
- Battery charger
Shipping[edit]
The car is now complete and will be shipped to the customer who ordered it.
References[edit]
- ^ a b c d e f g h i j k "How the Tesla Model S is Made , Tesla Motors Part 1". Wired.com. WIRED. Retrieved 1 April 2015.
- ^ a b c "How Tesla Builds Electric Cars , Tesla Motors Part 2 (WIRED)". Wired.com. WIRED. Retrieved 2 April 2015.
- ^ a b c d e f g "Electric Car Quality Tests , Tesla Motors Part 3 (WIRED)". wired.com. WIRED. Retrieved 2 April 2015.
- ^ Sibley, Lisa (2010-10-27). "Tesla officially replaces NUMMI in Fremont".
- ^ Danny King (2012-12-13). "Tesla will assemble, distribute vehicles in Holland for European market". Autoblog Green. Retrieved 2012-12-23.
- ^ Michiel Willebrands (2013-08-22). "Tesla opent assemblagecentrum in Tilburg" (in Dutch). Auto Week Netherlands. Retrieved 2013-10-07.
{{cite web}}
: Unknown parameter|trans_title=
ignored (|trans-title=
suggested) (help) - ^ a b c d e f g h i j k l m n o "How Its Made Dream Cars Season 02 Episode 10 Tesla Model S". How Its Made. Retrieved 2 April 2015.
- ^ Musk, Elon (2013-10-04). "Model S Fire". Tesla Motors. Retrieved February 20, 2014.
- ^ Cunningham, Wayne (2010-10-06). "Tesla Model S: The battery pack". C|Net. Retrieved February 20, 2014.
- ^ stopcrazypp. "NHTSA Opened Up the Model S Battery Pack - Pics". Tesla Motors Club Forum. Retrieved February 20, 2014.
We know from the diagnosis screen that the 85 kWh pack has 16 modules with 6 groups in series (so 96 groups in series): [1]
{{cite web}}
: External link in
(help); line feed character in|quote=
|quote=
at position 125 (help) - ^ a b US patent 8286743, Rawlison, Peter Dore, "Vehicle Battery Pack Ballistic Shield", issued 2012-10-16
- ^ US patent 2007009787, "Method and Apparatus for Mounting, Cooling, Connecting, and Protecting Batteries", issued 2007-1-11
- ^ Beltran, Balbino A.; Dunlap, Michael L.; Richardson, Frank D. (2013-08-07). "REPORT NUMBER: NCAP305I-KAR-13-054 NEW CAR ASSESSMENT PROGRAM (NCAP) FMVSS NO. 305 INDICANT TEST TESLA MOTORS, INC. 2013 TESLA MODEL S 5-DOOR HATCHBACK NHTSA NUMBER: MD5001" (NCAP305I-KAR-13-054). U.S. Department of Transportation, National Highway Safety Adminitstration: A-13. Retrieved February 20, 2014.
{{cite journal}}
: Cite journal requires|journal=
(help) - ^ Josie Garthaite (2012-06-23). "Leaving Baggage On the Dock, a Flagship Departs From California". The New York Times. Retrieved 2012-06-24.
- ^ "Charge your Model S - Adapter Guide, High Power Charging, and Supercharge". Tesla Motors. Retrieved 2012-06-23.
- ^ Chris Woodyard (2012-06-23). "First Drive: Tesla's Model S electric is spectacular". USA Today. Retrieved 2012-06-24.
- ^ Fisher, Thomas. "What Goes Into A Tesla Model S Battery--And What It May Cost". www.greencarreports.com. Green Car Reports. Retrieved 25 March 2015.
External links[edit]
- Tesla Motors official website
- Tesla factory behind the scenes documentary films
- How the Tesla Model S is Made, Tesla Motors Part 1, WIRED
- Tesla's Vice President of Vehicle Engineering, Peter Rawlinson, talks about some of the features of Model S engineering.
- High Efficiency Electric Drive Unit, Tesla Motors
- Tesla Motors patents
[[Category:Production and manufacturing]] [[Category:Tesla Motors]] [[Category:Automotive industry]] [[Category:Battery electric cars]] [[Category:Rear-wheel-drive vehicles]] [[Category:Sports sedans]] [[Category:Tesla Motors vehicles|Model S]] [[Category:Electric sports cars]] [[Category:Vehicles introduced in 2012]]